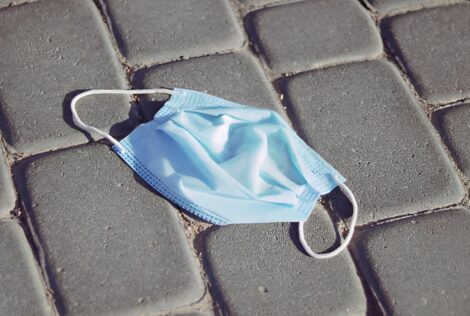
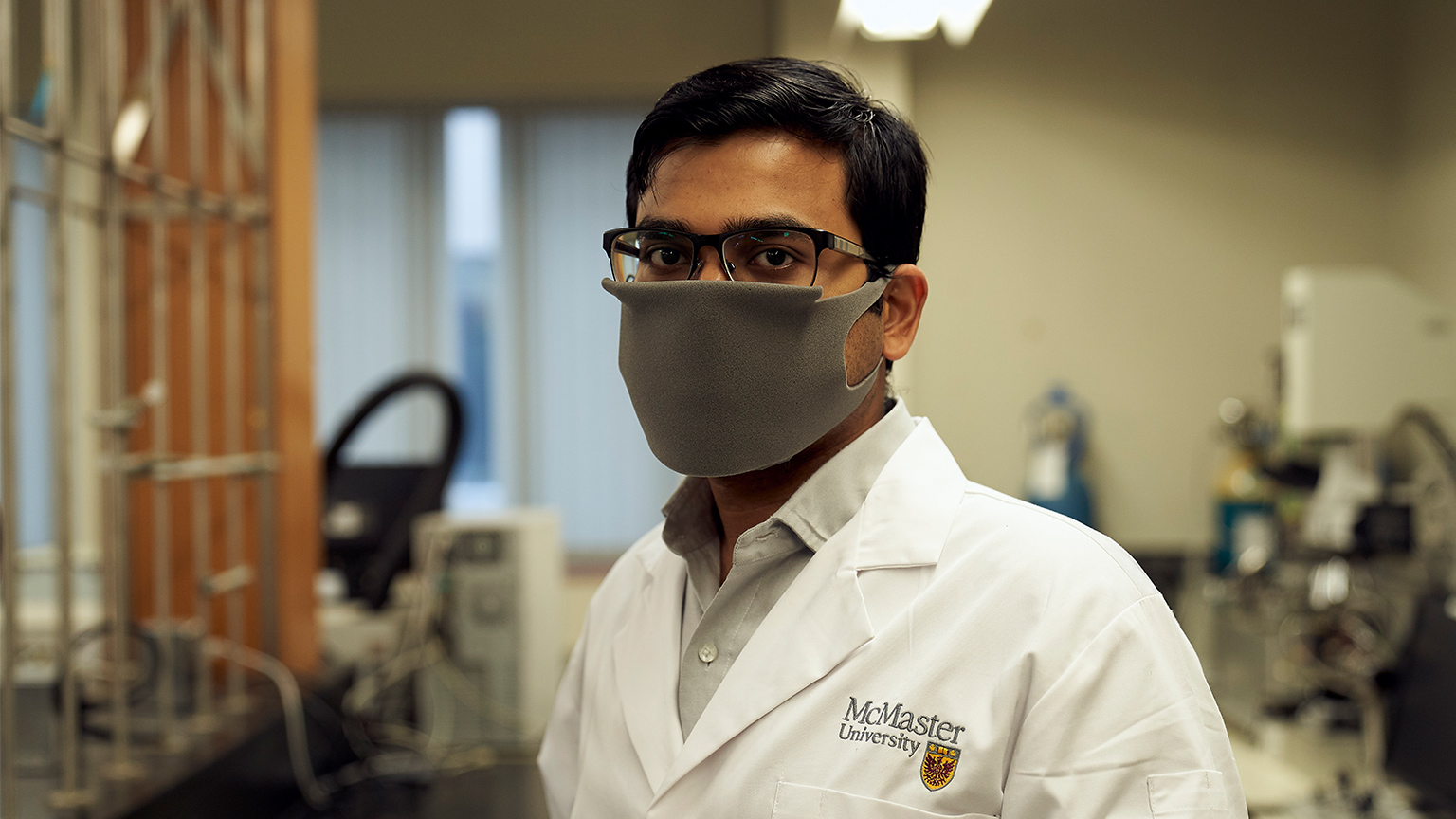
In the first part of the “Mac Eng arms the frontlines” series, we take a look at masks.
Faculty, staff and students across McMaster Engineering have turned their focus on creating solutions to combat the shortage of personal protective equipment (PPE) for local healthcare workers.
In addition to joining other faculties last week in a large donation of supplies to local hospitals, McMaster engineers are designing and testing mask prototypes which can be made locally.
This comes amid a call from the federal government for homegrown solutions to increase “desperately needed” equipment in the fight against COVID-19.
Overseen and coordinated by John Preston, Associate Dean of Research & External Relations and Ishwar K. Puri, Dean of Engineering, teams are working with manufacturing companies, government partners and local healthcare professionals with the goal of soon getting these prototypes to the frontlines.
“There are close to a hundred individuals across the faculty – faculty, staff members and students – involved in these activities, some remotely and others in labs across campus,” says Puri, calling the collective efforts “large and heroic.”
The efforts are being coordinated by the office of the Associate Dean of Research, virtually connecting teams working on similar projects.
“There’s never been this kind of putting aside of egos and willingness to stretch outside of people’s comfort zones,” Preston told the CBC on Monday.
This story is part of a series looking at different ways MacEng arms the frontlines. Here’s the latest on the faculty’s mask projects.
Our McMaster Engineering researchers step up: Surgical and N95 masks
What is it?
A group is on track to having L3 surgical masks and N95 mask prototypes ready for manufacturing. They’re building a personalized-fit N95 mask adaptor that will seal better to faces to prevent leakage.
Who is involved?
The Masks@Mac project is by mechanical engineers Rakesh Sahu, Suvojit Ghosh and Ravi Selvaganapathy. Research engineer Dariush Firouzi has been key to developing the mask designs.
They’re working with Dr. Alison Fox-Robichaud, a staff physician at Hamilton Health Sciences (HHS) and a professor in McMaster’s department of medicine, who is testing the masks away from patients and providing real-time feedback.
Chemical engineers are also instrumental in the testing process, including David Latulippe, Charles de Lannoy and Zeinab Hosseini-Doust.
Engineering physics professor Qiyin Fang, respiratory medicine physicians Imran Satia and Kieran Killian, and three engineering students are working to further the N95 mask design.
Niko Apparel, a Hamilton-based custom apparel company has stepped up to offer manufacturing services for surgical masks. They’ll be able to make about 5,000 masks per day for local hospitals.
APC Filtration, a Brantford-based air filter equipment manufacturer is providing in-house pressure drop and aerosol rejection testing for the masks.
What is the status?
The surgical mask design has been developed and tested, and the team is currently gathering test data to ensure the designs pass ASTM standards. Once produced by Niko Apparel, it will be sent to HHS.
The N95 mask’s first prototype was built and tested on March 28 and the next iteration of the design will be completed by April 7 – with the goal to produce locally within two to three weeks.
“I am proud of the contributions that all members of the team are making, as well as the interdisciplinary collaboration – both within engineering and between health sciences and hospitals,” says Selvaganapathy.
Supporting industry making foam masks
What is it?
McMaster is providing prototype testing for masks made by two auto parts manufacturers that are venturing together into mask production.
Who is involved?
A major auto parts manufacturer reached out to work together with McMaster with the goal of manufacturing millions of masks per week.
Flavio Volpe, president of Automotive Parts Manufacturers’ Association (APMA), met John Preston at the McMaster Innovation Park parking lot over the weekend to exchange prototypes.
“Many of us are working to produce more masks and respirators. The first priority is healthcare workers. Then confirmed or suspected COVID patients being cared for at home. The infected person should wear a mask. Thanks to [Flavio Volpe] for today’s progress,” Preston shared on Twitter after Sunday’s exchange.
Read more about the swift collaboration in this CBC article.
What is the status?
McMaster researchers received a new batch of updated samples on Monday. They are currently testing the prototypes and refining them.
Our students get involved: The Amanda Mask
What is it?
Amanda Tomkins, a third-year iBioMed and electrical & computer engineering student, put forward a promising design for part of the N95 mask – a soft ring that follows the outline of an N95 mask to seal the outer edges of the face, forcing all air through the surgical mask.
This was in response to a call-out for student volunteers for COVID-19-related initiatives.
“My sister is currently a nursing student, so she helped a lot with input into the design,” says Tomkins.
“My proposed design follows a similar shape to an N95 mask, however it goes from the bridge of the nose and under the chin and contains a jaw/face flap on both sides to prevent slipping when [the healthcare worker] is talking.”
Who is involved?
Qiyin Fang and John Preston are overseeing the student volunteers on this project.
Respiratory medicine physicians Imran Satia and Kieran Killian, along with medical physicist Joseph Hayward are collaborating with the team to provide testing and design feedback. They’re also members of the faculty of health sciences.
“This project will lead to a reusable personalized N95 mask with perfect fit and seal to protect frontline healthcare workers,” says Fang.
“It will also be environmentally friendly with very few single-use disposable components.”
What is the status?
The design for a tight-fitting N95 mask has been developed and is currently being refined for a second version. The team will then source the right materials suitable for N95 filtration and finalize testing.
Work with us! Find out how you or your organization can get involved