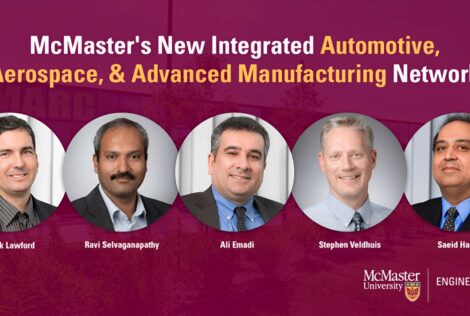
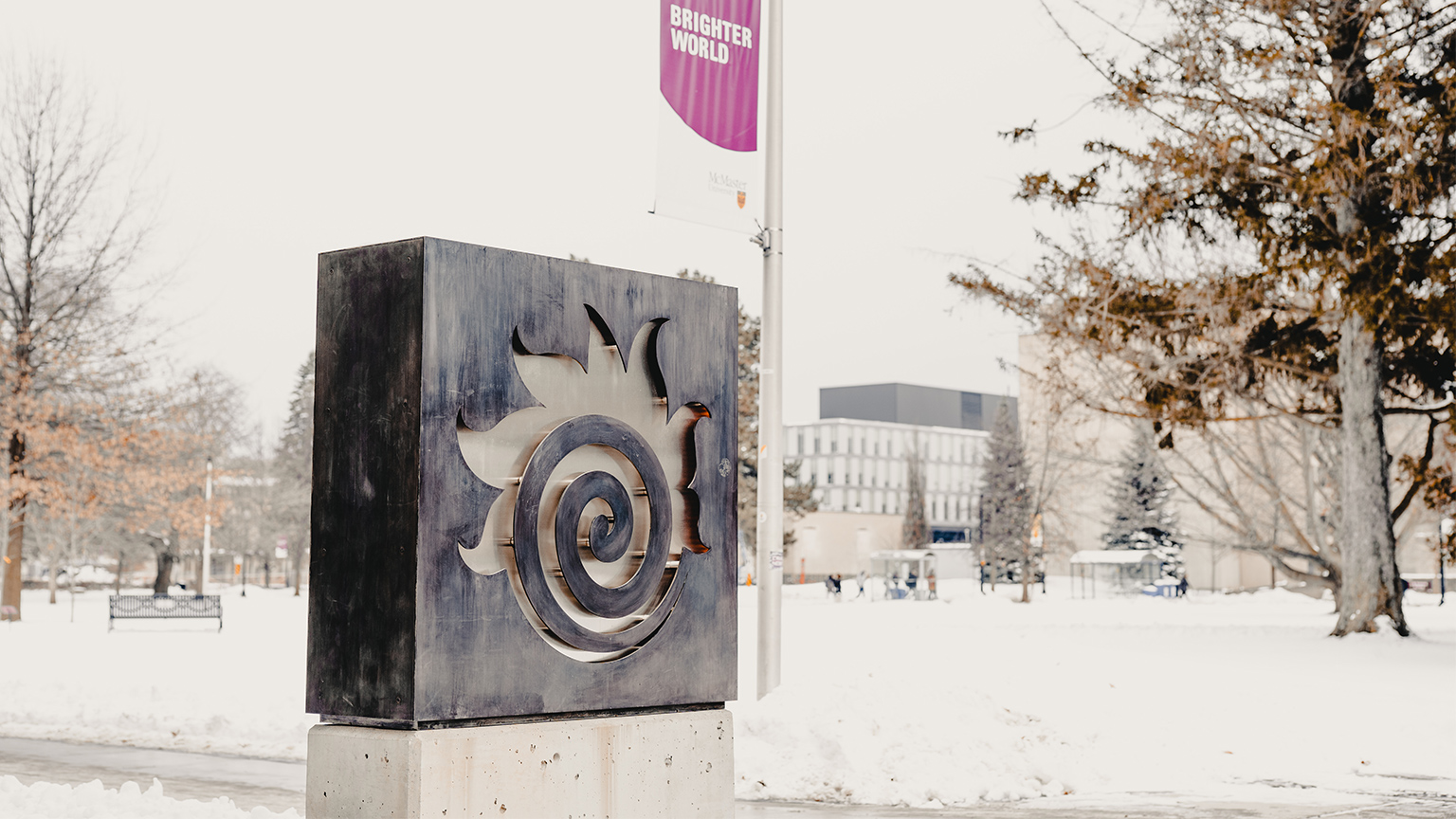
Stephen Veldhuis, director of the McMaster Manufacturing Research Institute and a mechanical engineering professor, caught the manufacturing bug early in his engineering career, machining parts at a summer job as an undergraduate.
“The old machinist who was looking out for me said that if I got any closer to the equipment my nose would get caught,” he chuckles. “I was just really fascinated – and that fascination led to trying to understand it more, and that became a career.”
Veldhuis still has his nose – and now he and his research team play a key role in helping keep Canada’s manufacturing sector competitive.
In the world of modern manufacturing, there’s a lot riding on parts that are often no bigger than a matchbook.
Millions of dollars. Jobs. Entire industries. Tiny variations in industrial processes can mean the difference between a multi-million-dollar contract for a Canadian company and watching local jobs and opportunities vanish to overseas vendors.
That’s why Veldhuis and his team focus their research on tribology, the study of friction and wear. As they develop an understanding of the physics behind the wear and tear that accompanies industrial machining, they can use those findings to propose more efficient processes and design tools that last longer and perform better. And those tiny parts are important.
“You can imagine a machine bigger than this room, but it still comes down to this little bit,” explains Veldhuis, holding up a component about the size of a Dinky car. “One little corner is what does all the work – so we put a lot of our engineering into trying to get the best performance out of that corner.”
That kind of work requires time, equipment and expertise – luxuries that many companies no longer have, as in-house R & D departments get downsized or phased out completely in the name of “lean” manufacturing. Instead, companies are focused on producing as much as possible, as fast as possible, with as little variation as possible.
If you want a competitive advantage, you have to operate at better levels than anyone else. Companies are no longer able to experiment, to make a mistake and learn from it and move on. There’s simply no margin for error.
That’s where MMRI comes in.
Unlike many university research groups, MMRI works closely with industry partners, largely in the automotive and aerospace sectors, to address real-life challenges. Once a problem is presented, researchers are able to model behaviours of materials and processes, test out improvements on industry-scale equipment and finally provide a solution that can move from the shop floor to production quickly.
“When you’re producing parts, you’re trying to minimize variation, which means you don’t learn much,” Veldhuis says. “I don’t have the pressure of having to ship 1,000 parts tomorrow, so we can go in and try different things based on our research and past experience. And that leads to innovation and improvement.”
Bettering their drilling process for these parts is what led voestalpine Rotec Summo Corp. (vRSC) to the McMaster Manufacturing Research Institute (MMRI) this past year. Thanks in part to the process improvements and subsequent cost savings provided by the university research team, vRSC is now the largest world-wide supplier of side-curtain airbag inflator bottles —the 30-cm long cylinder that’s filled with compressed gas and rests inside a vehicle’s airbag at the ready for deployment.
Working with MMRI, vRSC was able to improve the performance of its $50 carbide drills from 500 drilled holes to 10,000 holes – an improvement of a whopping 1,900 per cent.
Veldhuis points out that the benefits to working on real-world industry problems flow both ways: companies become more competitive, and MMRI researchers, including students, get relevant training and exposure to a wide variety of complex problems – not to mention the satisfaction of seeing the practical application of their work.
MMRI will be highlighting its recent results and capabilities at the annual Manufacturing Forum and Industry Open House on May 9. With the federal government focusing intently on innovation and economic growth with programs like the new Innovation Supercluster Initiative – a $950-million investment in high-value innovation partnerships –MMRI’s work is of particular interest to many stakeholders.
And while “innovation” is a popular buzzword these days in both government and industry, for Veldhuis the open house is a chance to highlight MMRI’s well-established track record and its long-standing expertise.
“We’ve been focusing on manufacturing for a long time, and our students have a high level of ability and provide a lot of value,” he says. “Advanced manufacturing is all the rage right now, but we’ve always been here.”