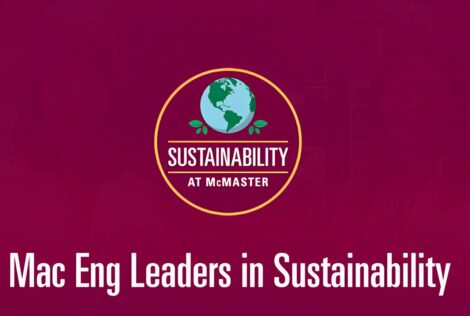
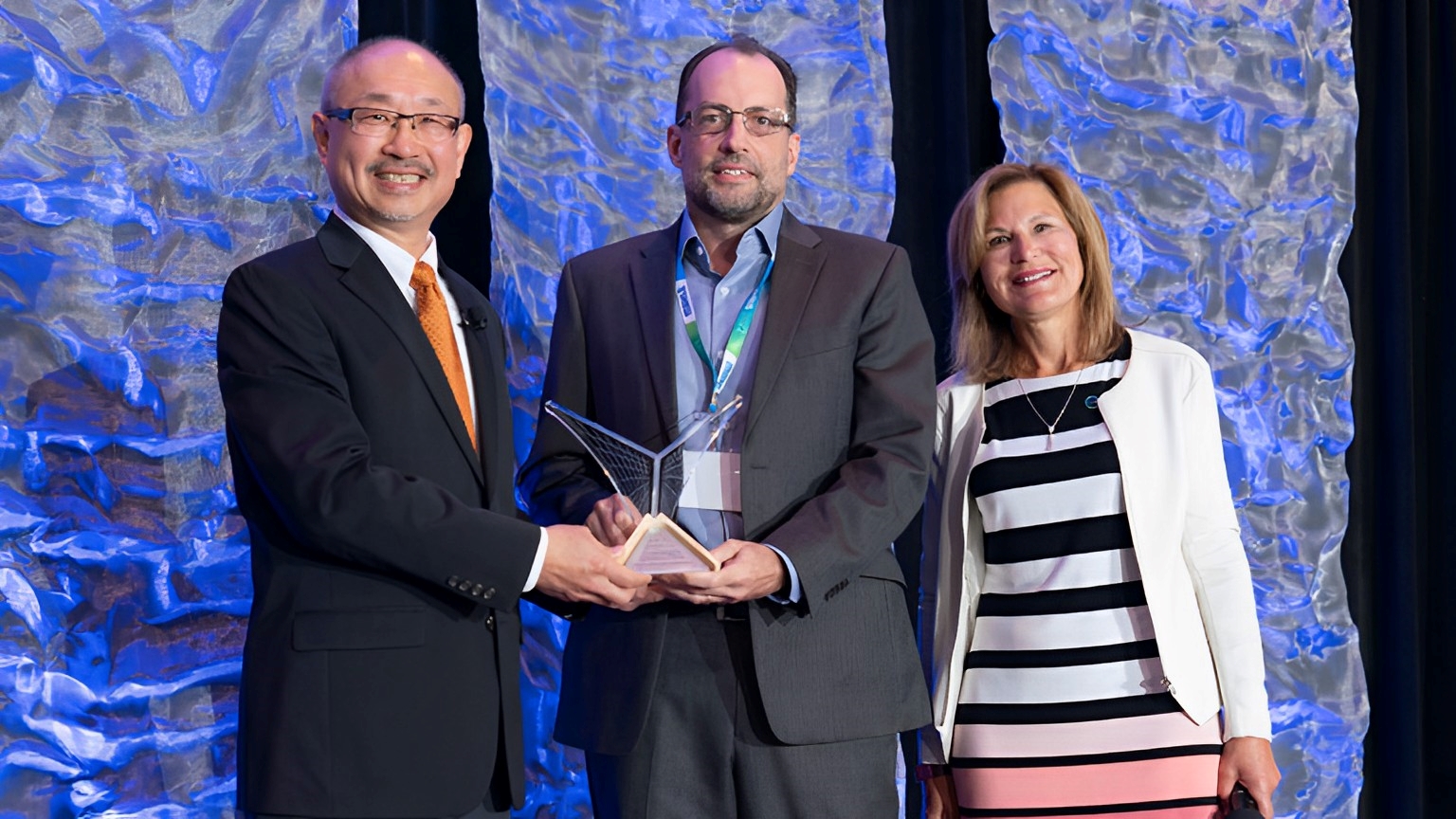
Sumanth Shankar always knew that tomorrow’s vehicles couldn’t rely on yesterday’s materials.
That reasoning led the mechanical engineering professor to reimagine the aluminum die casting alloy used in the automotive industry for decades.
His work has led to the development of a brand-new family of alloys that bonds aluminum with iron to create a high-strength material at least 35 per cent lighter than a traditional aluminum alloy.
The new material is the product of a successful collaboration among McMaster researchers, industry partner Nemak and the federal government’s CanmetMaterials Technology Laboratory (CMAT), says Sumanth.
Sumanth and research scientist Xiaochun Zeng share credit for the invention of the material.
Its potential impact on the industry was recognized in August with a prestigious Altair Enlighten Award 2022 in the category of Future of Lightweighting.
Presented in conjunction with the Michigan-based Center for Automotive Research (CAR), the awards recognize advancements that reduce vehicle weights to save fuel, reduce costs, improve efficiency and lead to a more sustainable automotive future.
“Aluminum alloys were innovated for net shaped castings during our war efforts in the early 20th century and everyone just kind of tweaked them for automotive needs since then,” explains Sumanth.
We decided to look at redesigning this material with an eye to what we really need to make these car parts as we move toward decarbonizing the industry.
Described as a smart, simple and sustainable alloy alternative, the Nemalloy (novel lightweight automotive aluminum alloy) is anticipated to make its way into a new generation of battery electric and internal combustion engine vehicles in the coming months.
Sumanth worked in partnership with automotive manufacturer Nemak, a leading global supplier of aluminum components for powertrain, e-mobility, and structural applications, to prepare the next-generation alloy for the market.
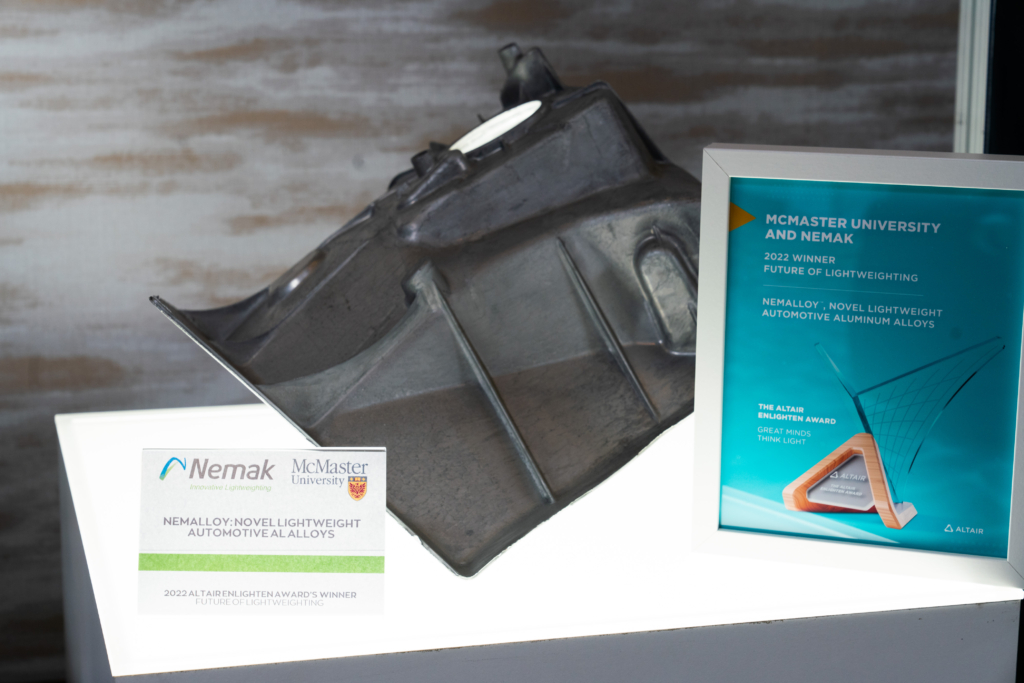
“Nemak’s purpose centers on driving lightweighting innovation and technology for the advancement of a more sustainable human mobility,” said Armando Tamez, Nemak’s CEO. “This award reflects our commitment toward contributing to the conservation of the environment and the wellbeing of society.”
Beyond its reduced weight, Nemalloy also offers other environmental benefits. Its composition eliminates the need for strengthening via heat treatment, significantly reduces manufacturing and process maintenance costs, is easily castable into ultra-large thin-walled components and is fully recyclable.
Significant investment from CanmetMaterials, which has been based out of McMaster Innovation Park since 2011, was integral to making the alloy a reality, Sumanth adds.
“Without their collaboration, none of this would have happened.”
John Preston, McMaster engineering’s associate dean of research, innovation and external relations, applauds the collaboration.
“The Nemalloy success is a demonstration of the great things that can happen when we bring together McMaster’s research facilities with industry expertise and government investment in technology and innovation,” he said. “We’re creating sustainable materials solutions that strengthen the competitiveness of our automotive industry.”
Following his success with Nemalloy, Sumanth and partners are launching a four-year transdisciplinary collaborative project to explore new technologies and alloys for structural automotive castings.