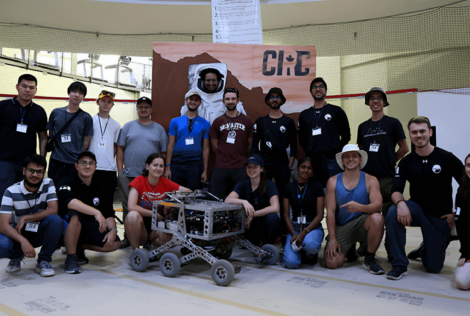
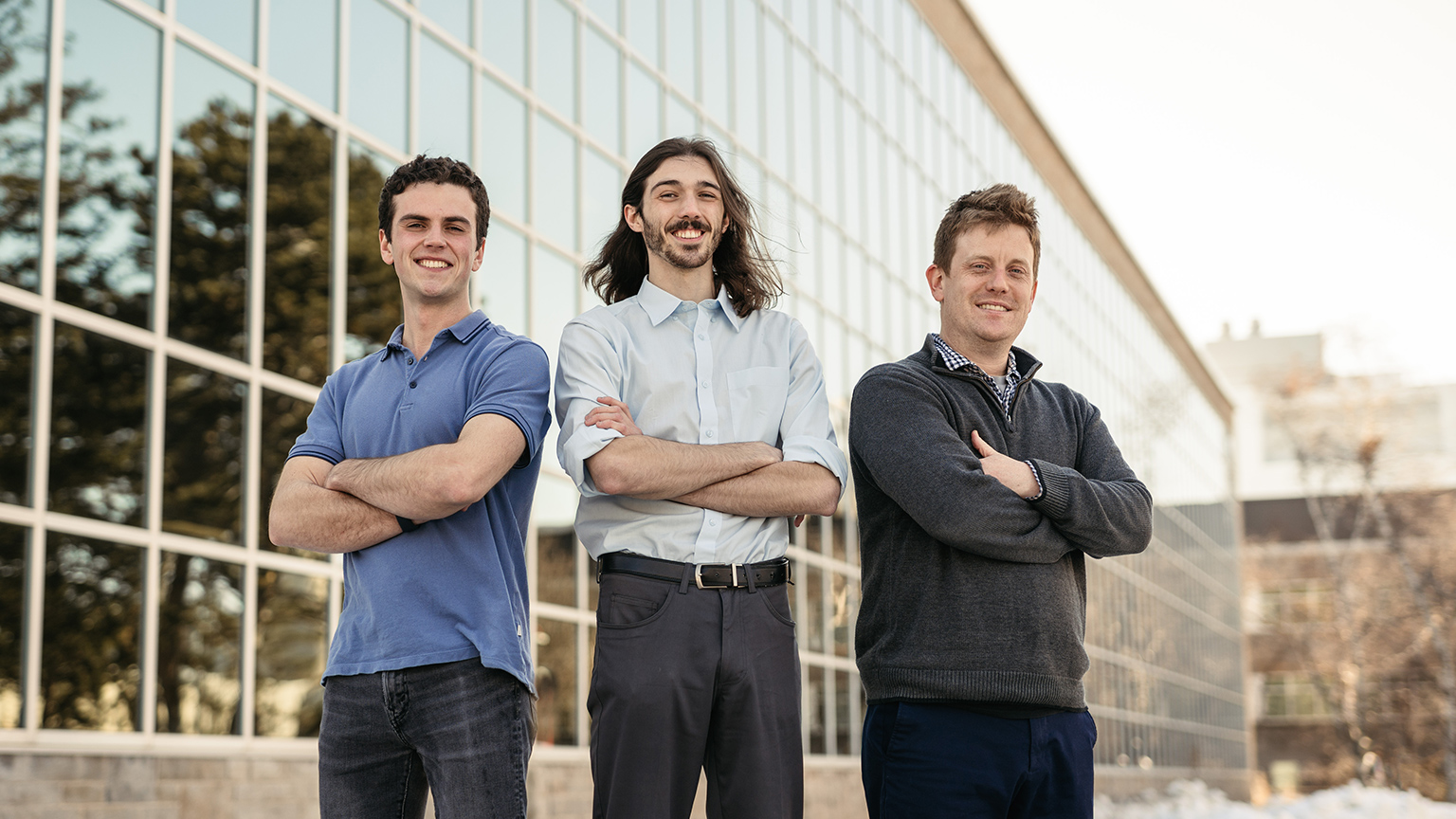
McMaster researcher Andrew Gadsden and his team of experts have worked with NASA to build an autonomous, robotic telescope mount to help create more accurate climate change models.
The 2021 Robert H. Goddard award winning airborne lunar spectral irradiance mission — air-LUSI —will send a telescope into high-altitude flight to measure reflected moonlight with unprecedented accuracy.
These measurements will be used to improve the calibration efforts of NASA’s Earth-observing satellites.
But to make sure these precise measurements more accurate, they need the telescope to be able to withstand high altitudes, extreme cold and constant motion.
That’s where Gadsden’s team comes in.
CODENAME: ARTEMIS
The first-generation robotic mount that Gadsden’s team built — named ARTEMIS, short for the Autonomous, Robotic TElescope Mount Instrument Subsystem — was designed to ensure the telescope stays trained on the Moon while in flight.
NASA’s air-LUSI telescope will be integrated to the mount, and the United States National Institute of Standards and Technology (NIST) and United States Geological Survey (USGS) will use the measurements it collects to help develop models that are used to fine-tune NASA’s Earth-observing satellites. This calibration will help ensure the data they collect is exceedingly accurate and precise.
And why track the Moon in the first place?
The data from satellites that record conditions on Earth are affected by the atmosphere, local conditions and climate.
Because the Moon is relatively stable and unaffected by these factors, its light can serve as a benchmark for Earth-observing satellites.
“These satellites, among other sensors and sources, are vital to studying our planet in order to accurately predict and track the consequences of climate change,” says Gadsden, an associate professor of mechanical engineering.
NASA will use the data collected by their Earth-observing satellites to better understand what is happening here on Earth. This knowledge will then be used to build more accurate climate change models.
“This project is at the intersection of science and engineering,” says Gadsden. “We are providing the engineering tools to collect all this data and then we pass the results of that off to science to analyze the data and understand what it means and how to initiate change from it.”
A TRICKY MANOEUVRE
From an engineering perspective, explains Gadsden, ARTEMIS is no ordinary telescope mount.
“There are performance and design constraints, there are physical constraints and there are environmental constraints,” says Gadsden.
For starters, the telescope they’re building this mount for will be flying at an altitude of approximately 70,000 feet and will be operating within the wingpod of an old Soviet-era spy plane.
Given that the telescope is deployed above roughly 95 per cent of Earth’s atmosphere, the mount also needs to be built to withstand temperatures of around -60 degrees Celsius.
To remedy these issues, Gadsden explains, their mount was built in-house with a double gimbal control mechanism that corrects for aircraft and lunar motion during flight, ensuring that the telescope tracks its target at all times.
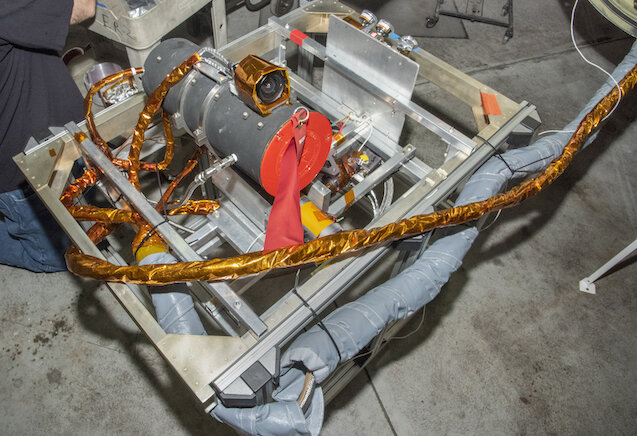
The uniqueness of the system requires that the design, analysis, rapid prototyping and fabrication is all done in-house at McMaster.
“There’s a lot of custom work on this mount,” explains Andrew Newton, a research engineer in Gadsden’s lab. “It’s not built with off-the-shelf components. Almost everything is custom engineered.”
“This process really streamlines the development and gives us confidence that what we’re building is going to work.”
HAAMR TIME
To date, Gadsden’s team has flown their mount on over 10 high-altitude flights to test its functionality and reliability.
These tests determined that ARTEMIS was highly effective in stable conditions, but its accuracy fluctuated when the plane encountered turbulence, creating corrupted or uncertain measurements.
“At 70,000 feet the aircraft is fairly stable, so the control system doesn’t need to work that hard,” says Newton. “But when we do run into turbulence, the control system isn’t able to compensate for that.”
Part of the issue, explains Newton, is that the telescope came in at a heavier weight than they designed their actuators to account for.
That’s why Gadsden’s team is currently working on a second-generation instrument, called the High-Altitude Aircraft Mounted Robotic (HAAMR) telescope mount.
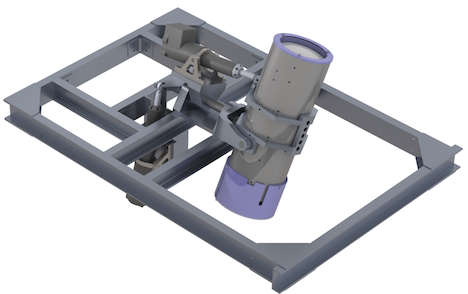
The new design addresses several performance issues related to movement, Gadsden says, and the team is working to improve its tracking response during turbulence.
“Although we met the original tracking performance objectives, we knew that we could do even better, particularly during turbulent flights,” says Alex McCafferty-Leroux, mechanical engineering graduate student and member of Gadsden’s team. “With our proposed modifications, we should be able to double our tracking accuracy and maintain target lock during bumpy portions of the flights.”
HAAMR will be delivered to the team at the United States National Institute of Standards and Technology (NIST) in Gaithersburg, Maryland in July for integration with their telescope.
In January, HAAMR will be deployed to NASA’s Neil A. Armstrong Flight Reseach Center (Palmdale, California) for an extended air-LUSI Operational Flight Campaign.
A WORLD OF POSSIBILITY
The scientific impact of the air-LUSI project is limitless.
With the potential to create much stronger climate change models based on more precise measurements, this calibration model is of significant interest to European, American and Canadian space agencies.
And with more precise measurements come even more exciting opportunities.
“With better data, there’s the potential to apply machine learning to predict what’s going on with our planet,” explains Gadsden.
“The information collected from the satellites will be used to better study our planet’s health in order to protect biodiversity and, consequently, human health.”