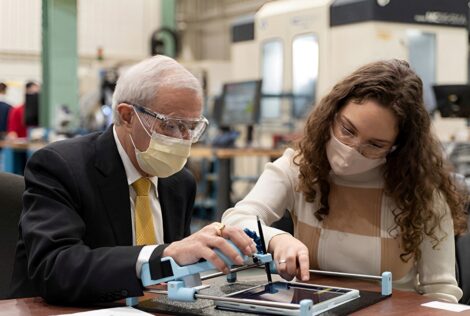
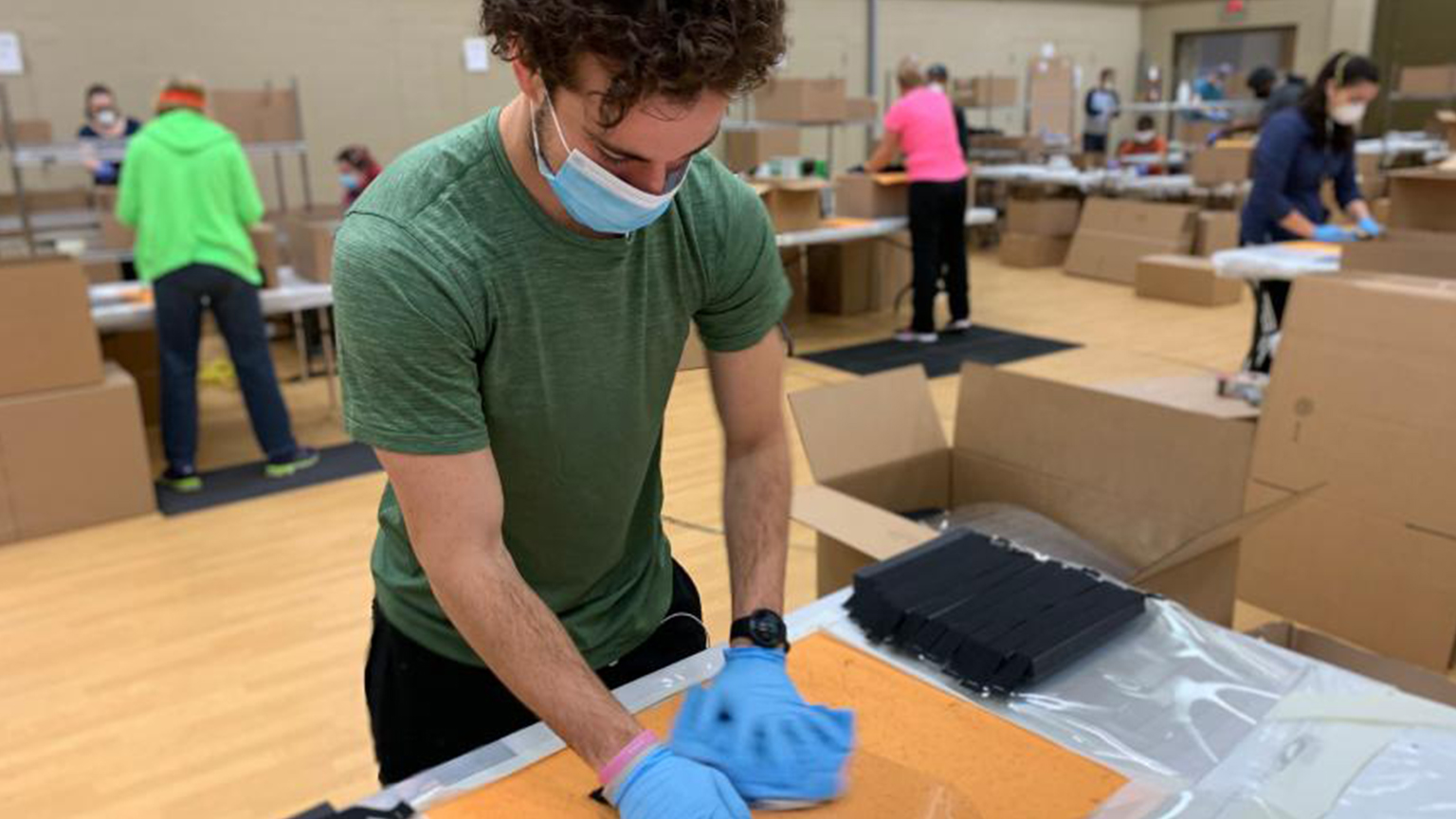
When COVID-19 struck Hamilton in March, the McMaster Manufacturing Research Institute (MMRI) team rallied to help the community design and manufacture protective gear and medical supplies. A month later, they’re working closer than ever with local hospitals and manufacturers.
On a typical week, in pre-COVID-19 times, the McMaster Manufacturing Research Institute (MMRI) team is busy working on new tools and processes for companies with challenges on their production side.
The team uses its research expertise to help companies stay ahead of the “disruption curve” – supporting automotive and aerospace and other industries navigate technological change.
The MMRI team immediately shifted their manufacturing expertise to work within the medical supply chain. They have been constantly pivoting to help hospitals and manufacturers meet the needs of the crisis ever since — from protective gear and medical supplies like ventilators, face shields and, their latest focus, plexiglass guards.
For our industry partners, we’re looking at improving their productivity, reducing their costs, and helping them improve their products. That was something we were naturally doing, and now with COVID-19, we’ve been able to really focus on medical applications.
Upon hearing about ventilator shortages abroad, the team initially made a simple ventilator prototype which could be mass produced quickly.
“As it turns out, the Canadian government initiated a large order with companies already making ventilators, so that demand subsided,” says Veldhuis, who oversees a team of 28 engineers, technicians and students.
The team then pivoted again. This time, to make face shields.
Working together with Whitebird, a Hamilton-based safety and shipping supplies company, they’re now producing thousands of protective face shields a day at several assembly areas, including a local gym.
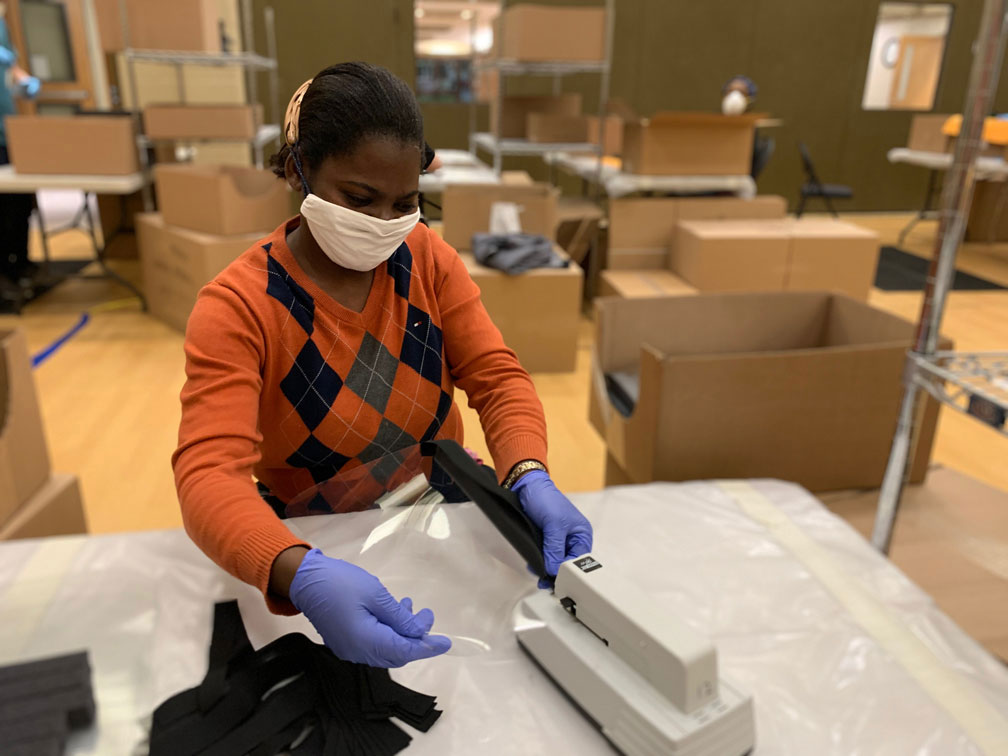
“In a few days, we knew we could do it and Whitebird threw their whole weight behind the idea. We spent the next two weeks nailing down a supply chain, setting up production and clearing regulatory hurdles” says Simon Oomen-Hurst, the MMRI’s program manager.
“We went from an idea to mass production in less than three weeks.”
The team is working on securing new areas for assembly to meet the continued growing demand for their products.
“These projects are highlighting how vital it is to be able to manufacture critical supplies domestically,” says Steve Remilli, project manager at the MMRI. “That’s a silver lining.”
Teaming up to help hospital and essential workers
A large part of the MMRI team’s efforts are now working with Hamilton Health Sciences (HHS) and St. Joseph’s Hospital to find solutions for the hospitals’ needs as more supply challenges arise.
“We’re working with the diagnostics group at Hamilton General Hospital to develop a mobile plexiglass guard for staff,” says Remilli. This plexiglass guard may be used by staff who perform ultrasounds on patients, for instance.
“We now need to be able to think about how all of these procedures [in hospital] can still be done while avoiding the spread of COVID-19,” says Veldhuis.
Every couple of days, Veldhuis says his team gets a request for a new item, and Brady Semple, a research engineer at the MMRI, works up a design and prototypes it. After the hospital reviews and approves the final design, it gets sent out for local manufacturing.
“That’s happening within days, so it’s working really well,” Semple says. “We’re trying to structure ourselves to be problem-solvers and support delivery by working with our industry partners.”
On the testing front, Veldhuis’ team is also working with St. Joe’s Healthcare to source “critical supplies” for COVID-19 test kits to increase testing capability in Canada.
These are complex problems, Veldhuis says, and the team has been working with experts including David Bulir (St. Joe’s), Heera Marway (MMRI), Carmen Andrei (Canadian Centre for Electron Microscopy), Kirk Green (McMaster Regional Centre for Mass Spectrometry), Rakesh Sahu (Multiphysics Research Group), Hooman Derakhshani (McMaster department of medicine) and Daniel Yang (Microstar, local McMaster startup) to develop solutions.
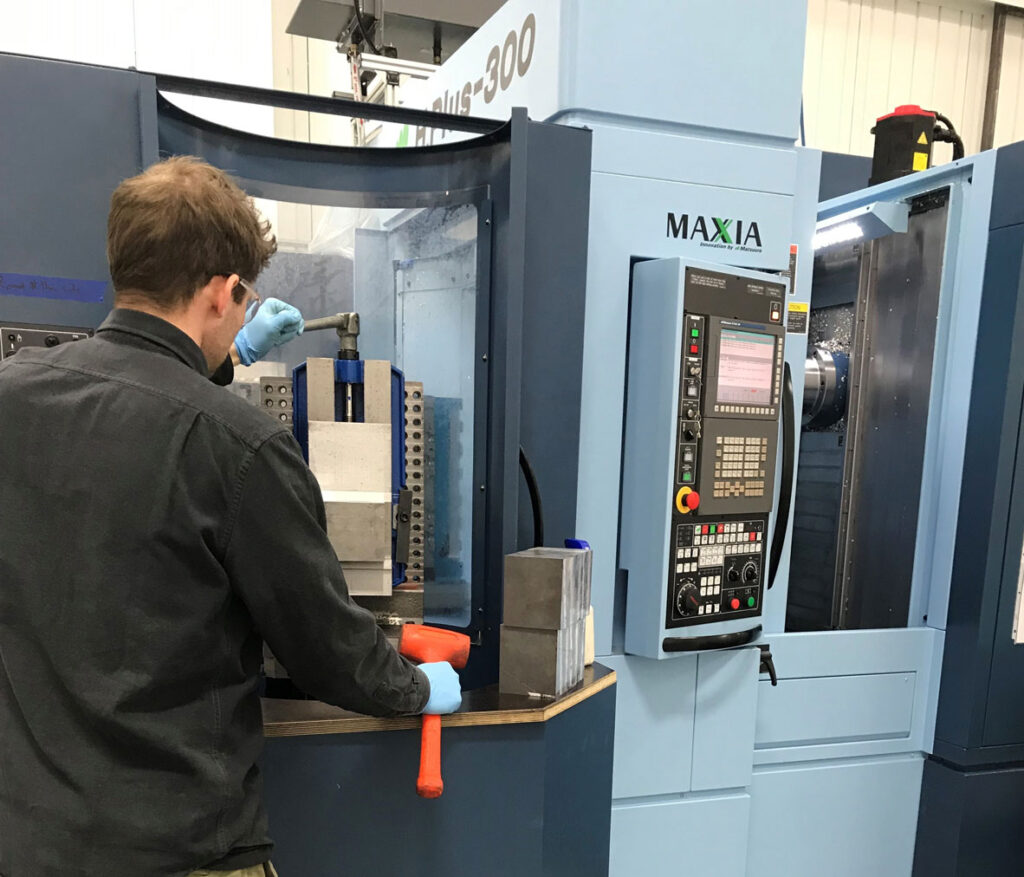
This work has progressed to the point where Jonathan Hornell-Kennedy at Coreprint Patterns is producing the molds needed to mass produce the supplies needed to expand testing.
“In addition to essential workers, solving COVID-19 needs input from scientists and a wide range of subject matter experts. Fortunately, McMaster has a strong, collaborative community that is well-positioned to help,” says Veldhuis. “When we look back at this time, we just want to know that we did everything we could and used all our resources to help.”
A natural change in direction
“From a technical perspective, this shift hasn’t been all that out of the ordinary for us. The need to manufacture PPE for COVID-19 response has fit well into our staff’s wheelhouse,” says Oomen-Hurst.
“Barriers you’d run into during ‘normal’ times have evaporated. Everyone did everything they could to help.”
Veldhuis says his team was able to hit the ground running on these projects with help from funding from FedDev Ontario‘s program, SONAMI, which brings together resources from Niagara College, Mohawk College, Sheridan College, Lambton College, Fanshawe College, Conestoga College and McMaster.
The MMRI team also works in close collaboration with Western University and the University of Waterloo as part of the Ontario Advanced Manufacturing Consortium. The three universities are currently sharing supplies of critically needed materials and expertise to complete high-priority COVID-19 projects.
With funding support from these agencies, Veldhuis says they had the team in place and the resources to initiate these projects “right away.”
“More than anything, I’ll remember how everyone pulled together to support fighting COVID-19, and what can be accomplished when we work together for a common goal,” Oomen-Hurst adds.